El desperdicio de energía puede ocurrir en cualquier parte y en cualquier momento en un entorno industrial: desde luces que se dejan encendidas y un control deficiente de la temperatura hasta motores ineficientes o máquinas que funcionan en vacío durante largos periodos de tiempo. Hoy en día, con la escasez de energía y el aumento de los precios del combustible, este desperdicio puede acumularse rápidamente y costar muy caro a las industrias en términos de su capacidad para mantener los niveles de producción o incluso para seguir funcionando.
Y, por desgracia, no parece que las cosas vayan a mejorar pronto, ya que se prevé que el invierno que se acerca será duro. La International Energy Agency (IEA) señala que Europa se enfrenta a un déficit de oferta y demanda de gas natural de 30.000 millones de metros cúbicos (bcm). Esto también tendrá graves repercusiones en el futuro abastecimiento de combustible para el invierno, debido a la lentitud con que se llenan ahora los depósitos de gas. Según el informe, «este déficit podría representar casi la mitad del gas necesario para llenar los almacenes al 95% de su capacidad al comienzo de la temporada de calefacción de 2023-24». Esta dura realidad pone de relieve la urgencia de que tanto los gobiernos como los consumidores industriales tomen medidas inmediatas para mejorar la eficiencia operativa y reducir al mismo tiempo el consumo de energía.
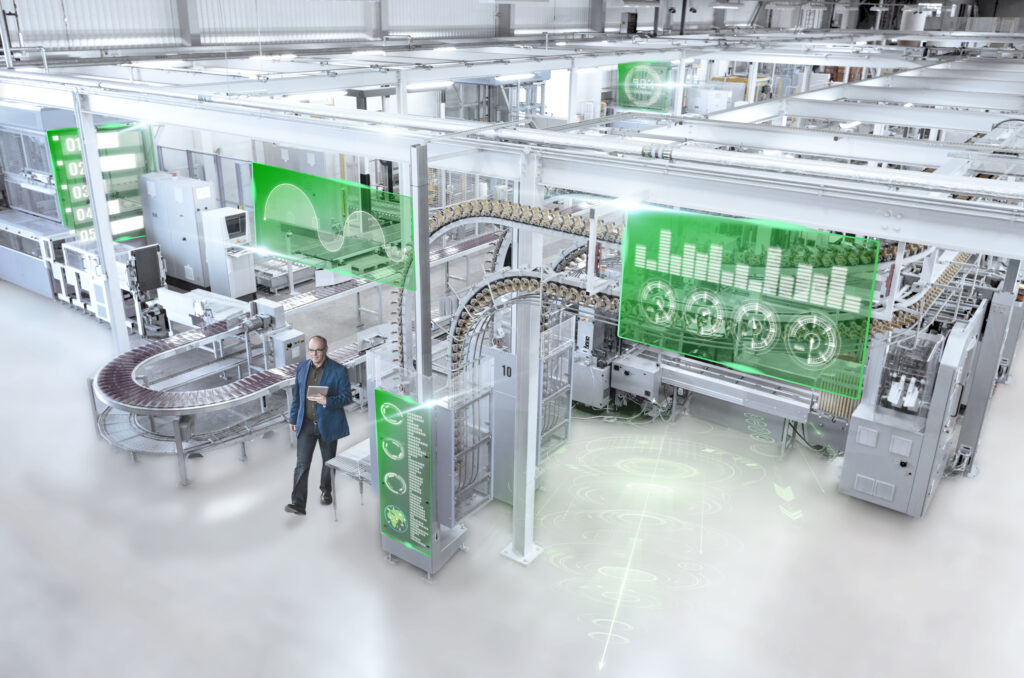
Pero, ¿cómo reducir el consumo de energía?
Ten en cuenta estas cuatro formas de aumentar rápidamente la eficiencia operativa y reducir el gasto energético:
- Medir el consumo: Realizar auditorías energéticas e instalar medidores fiables de la calidad de la energía son buenas formas de establecer puntos de referencia para elaborar un plan eficaz de gestión energética.
- Gestión activa de la energía: Las soluciones rápidas y rentables, como instalar variadores de velocidad o equipos de distribución eléctrica conectados y de alta eficiencia, pueden reducir inmediatamente la factura de la luz.
- Automatización: La automatización permite un control más preciso de los equipos y procesos para optimizar el consumo de energía sin comprometer los requisitos de producción. Puede regular parámetros como la temperatura, la presión, la velocidad y los caudales utilizando datos y análisis en tiempo real de los dispositivos conectados.
- Monitorización: un software fácil de usar puede identificar las tendencias del gasto energético y las áreas problemáticas para que puedan abordarse antes de malgastar el dinero. La gestión energética no es una operación aislada, sino un bucle de mejora continua.
Cómo liberar el poder de la automatización y la digitalización
Aplicar las capacidades complementarias de la automatización y la digitalización a los procesos y sistemas industriales puede suponer una gran diferencia en su eficiencia operativa, lo que, a su vez, puede reducir su consumo de energía. La automatización optimiza el uso de los procesos, la energía y los recursos reduciendo los residuos (agua, gas, aire, materias primas, etc.), mientras que la digitalización con software industrial es la base para hacer visible lo invisible. Al permitirle extraer datos significativos, puedes utilizar la inteligencia y la analítica para ver dónde existen ineficiencias en toda la cadena de valor y así poder eliminarlas. Esta potente combinación puede facilitar un nivel avanzado de control mediante:
- Cuadros de mandos que ayudan a gestionar de forma rentable los dispositivos inteligentes distribuidos (por ejemplo, sensores, luces o accionamientos de motor) en los principales procesos industriales. Las aplicaciones basadas en la nube cuestan menos y proporcionan datos más detallados que el seguimiento manual del consumo de energía para identificar mejor las nuevas oportunidades de mejora de la gestión energética. Un cuadro de mandos predictivo proporciona a los operadores información sobre las condiciones futuras y permite desarrollar estrategias proactivas para gestionar las decisiones de producción específicas de la energía.
- Visibilidad end-to-end unificada que te permite utilizar tus datos energéticos históricos para modelar patrones de consumo futuros. Estos datos capturados «what-is» permiten el modelado «what-if». AVEVA Centro de operaciones unificado, por ejemplo, proporciona esta capacidad y ayuda a romper los silos entre la gestión de la planta y la producción. La integración de la capa de control de automatización de la planta con las herramientas de productividad del operador proporciona a los operadores la información que necesitan para tomar decisiones más precisas y rápidas, limitando así los residuos, aumentando la eficiencia y optimizando el rendimiento.
- La integración de la gestión de la energía y la automatización de procesos, que tradicionalmente han funcionado como entidades separadas, pero la convergencia de ambas crea una solución que puede:
- Eliminar los silos de información y descubrir oportunidades de optimización del sistema que repercuten directamente en la eficiencia de la planta.
- Aumentar la responsabilidad del consumo energético en toda la red de la planta
- Mejorar el uso de la energía de proceso hasta en un 10%.
Un ejemplo de eficiencia energética
Las instalaciones de aguas residuales son grandes consumidoras de energía, por lo que maximizar la eficiencia operativa es una prioridad. Cuando Veolia Water se propuso construir una avanzada planta de tratamiento de aguas residuales dentro de un túnel en Punta Gradelle, en la costa italiana de Sorrento, necesitaba un sofisticado sistema de control que pudiera gestionar de forma eficaz y eficiente las complejas operaciones.
Una solución como EcoStruxure™ for Water encajaba a la perfección porque ofrecía una potente combinación de automatización de los procesos de la planta y gestión energética. La centralización y agregación de datos en tiempo real proporciona al equipo de operaciones una visión que les ayuda a tomar decisiones más informadas sobre la eficiencia energética, la fiabilidad de los equipos y las acciones de mantenimiento.
Al final, Veolia consiguió un importante ahorro del 15% en energía (y costes asociados) y una mejora del 20% en su eficiencia de producción. Gianfranco Favali, director del Departamento de Diseño de Proyectos de Veolia, calificó los beneficios obtenidos de «verdaderamente notables».
Para situar el ahorro de energía en un contexto más amplio, el Departamento de Energía de EE.UU. calcula que las depuradoras municipales estadounidenses consumen más de 30 teravatios-hora de electricidad al año, con un coste acumulado de unos 2.000 millones de dólares. Si tomaran medidas para reducir su consumo de energía en un 15% en general -reduciendo los residuos y mejorando la eficiencia operativa-, ¡se ahorrarían la impresionante cifra de 300 millones de dólares al año!
Para más información
Para saber más sobre las medidas que puedes tomar para reducir tu consumo energético industrial, descarga nuestra nueva guía, «Three smart actions to help industrial companies navigate the European energy crisis.»
Añadir comentario