Durante muchos años, los ámbitos de la operación y de la ingeniería dentro del sector industrial han estado completamente separados. En términos muy simples, el proceso de diseño, construcción y operación de una planta implicaba una serie de “entregas” de ingenieros a ingenieros. Alguien diseñaba los procesos, los entregaba a una empresa de ingeniería que diseñaba y construía la planta y al proveedor del control que diseñaba y programaba el sistema de control y, al final, se entregaba todo al usuario final para operar la planta. Bajo este modelo tan fragmentado, siempre ha sido un gran problema acceder y mantener la documentación actualizada para optimizar la eficiencia operacional y la rentabilidad de la planta, si no se trataba de algo impulsado por el propietario y el operador.
Con el actual software de diseño de procesos, el modelo ha cambiado. Todo se hace vía software, que se interconecta profesionalmente con el software de diseño que permite a los profesionales construir la planta y programar automáticamente el sistema de control. Es más, el resultado de esa herramienta de diseño sirve como una “representación digital” de la planta. Cuando la planta está online, la representación digital interactúa con los datos en tiempo real generados en la planta física. En este momento, el software transforma la “representación digital” en un “gemelo digital” que puede reflejar exactamente lo que está sucediendo en la planta física.
Un cambio en la dinámica del flujo de trabajo
Hasta hace poco, los trabajadores que operaban los sistemas clave de la planta solían utilizar solo una pequeña parte de la amplia funcionalidad de su software. La visualización era complicada y las funciones eran difíciles de aprender. Ahora, con un software operacional más avanzado e intuitivo, las tareas pueden realizarse fácilmente sin tener que entender todos los complejos detalles.

Si de repente reúnes estos dos aspectos (ingeniería y operaciones), ahora con el modelo 3D las alarmas muestran en la pantalla la bomba en 3D para que puedas ver virtualmente dónde está. Puedes ver virtualmente la bomba y a qué tipo de tuberías está conectada, si es una bomba redundante o qué tipo de válvulas necesitas operar para separar la bomba del resto del sistema. Y antes de que mandes todos estos datos a un ingeniero de servicio, él ya sabrá exactamente qué hacer. Todo el trabajo previo ya se ha hecho de forma virtual y también ha sido simulado virtualmente, siendo el último paso la ejecución del trabajo físico.
Si miramos un poco hacia el futuro, el trabajador de la planta que recibe la alarma ya no está sentado en frente de una pantalla, sino equipado con un juego de gafas de realidad virtual que muestran la representación 3D o el gemelo digital de la planta. El ingeniero de servicio también tiene su propio juego de gafas. En su caso, él ve la planta real, pero sus gafas contienen datos digitales que empiezan a entrar en su campo de visión y se mezclan con la realidad que está viendo. Está experimentando la realidad “mixta” o aumentada que le ayuda a llevar a cabo su reparación de forma más segura y ágil.
Intercambio de conocimiento y mayor eficiencia
Las implicaciones de estas tecnologías son muchas. En primer lugar, de una forma más intuitiva, puedes hacer un uso completo de capacidades que, quizás ya existían, pero que no eran utilizables por su complejidad y el grado de formación requerido. Ahora, incluso los usuarios con menos formación pueden acceder a algunas de estas funcionalidades.
En segundo lugar, las herramientas de desarrollo de software se han vuelto mucho más sofisticadas en términos de capacidades gráficas, capacidades de procesamiento y de flexibilidad sobre dónde se ejecuta el software.
Por todo ello, ya se usan mejor las herramientas y los profesionales trabajan de forma más intuitiva con sus equipos, sin necesidad de probar en el mundo real ni entender todos los detalles de fondo.
Encuentra más información sobre las soluciones de software industrial y de ingeniería líderes del mercado entrando aquí.
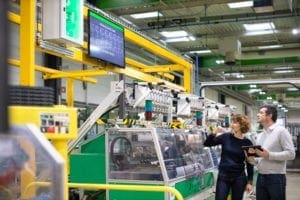
Añadir comentario