El suministro rentable y la optimización de la energía son fundamentales para el rendimiento de la planta y el retorno de la inversión en los procesos de alto consumo energético.
Con el incremento de la concienciación sobre la sostenibilidad, la mayoría de las empresas de petróleo y gas están tomando iniciativas para reducir el consumo de energía y la huella de carbono a través de informes de impacto ambiental y programas de optimización.
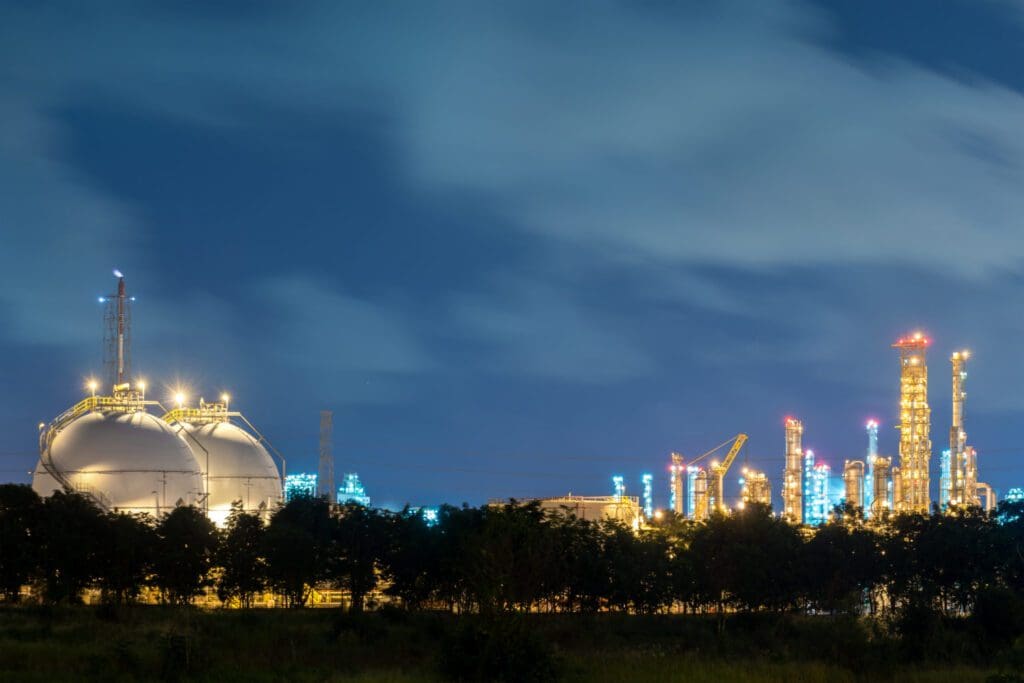
¿Por dónde comenzamos?
Tanto si se trata de un proyecto «brownfield» como «greenfield», en las primeras fases del diseño hay que abordar cuestiones importantes que buscan el equilibrio entre el consumo, la compra y la generación de energía para maximizar el rendimiento del activo.
En el caso de la energía eléctrica, por ejemplo, la cantidad de energía que se compra a la red, frente a la que se genera en las instalaciones, es un aspecto clave que tiene un gran impacto en el coste.
El uso de contadores para monitorizar el consumo de actividades específicas y unidades de proceso individuales permite alinear y ajustar la generación y el consumo en tiempo real.
Las características físicas y químicas del proceso determinan las interacciones entre la electricidad, el gas, el vapor y el agua fría. La optimización de los procesos energéticos consiste en gestionar las compensaciones entre estos tipos de energía a lo largo de los cuales se minimizan los costes y la huella de carbono de la planta.
Gracias a la integración de los procesos energéticos, los operarios reciben información en tiempo real sobre la eficiencia energética, lo que les permite tomar decisiones responsables.
La gestión energética optimizada aumenta la eficiencia del proceso al reducir el coste total de la energía en cada unidad de producción (por ejemplo, equilibrando las demandas de consumo de electricidad, gas y vapor).
El equilibrio entre las fuentes de energía se optimiza, y las partes interesadas de toda la empresa reciben información actualizada sobre el coste de la energía y el impacto en los beneficios debido a los cambios en las condiciones de funcionamiento. La fiabilidad y la rentabilidad de la planta aumentan a medida que el proceso y el equipo se alinean y optimizan para el consumo.
Sin embargo, en la actualidad las decisiones operacionales suelen basarse en observaciones periódicas de energía, informes de mantenimiento, fiabilidad, y eventos medioambientales, y no en tiempo real.
Además, la energía se gestiona separada de otro tipo de fuentes que también suministran al proceso y la instalación; sin embargo, según un estudio del sector industrial alemán realizado por Tallal Javied y otros publicados en 2016, los motores eléctricos suelen representar el 70% del consumo eléctrico de una planta.
Los operadores tienen una visibilidad y una responsabilidad limitadas en las decisiones que afectan al coste energético, al coste de los materiales y al valor del producto. Pero la mejor forma de abordar esta carencia es mediante una solución integrada de optimización de la energía de proceso que supervise y optimice las principales formas de uso de la energía.
3 tecnologías de base para la estrategia de optimización energética
Para lograr el objetivo de mejorar la eficiencia y la rentabilidad, la estrategia de optimización energética se basa en tres tecnologías:
- Un mecanismo analítico de Big Data para la obtención de datos del proceso y de la energía a partir del historial, aplicando la tecnología analítica para obtener información sobre el proceso.
- Un modelo matemático predice la mejor combinación de electricidad, gas o combustible y vapor que minimiza el coste por unidad de producción. El modelo incluye las eficiencias de cada pieza importante del equipo, como las turbinas de vapor, y prescribe el orden en que estas piezas del equipo deben dejar salir el vapor, por ejemplo.Un enfoque basado en el modelo permite una optimización energética en toda la planta que no se puede conseguir con los métodos de control más convencionales. El modelo suele utilizar el control predictivo multivariable (MPC) u otra forma de control avanzado de procesos (APC) y la optimización en tiempo real (RTO) que tiene en cuenta la interacción simultánea de múltiples entradas y salidas.
- Un modelo de visualización en tiempo real extrae los datos del proceso y la energía del histórico de la planta para medir el rendimiento financiero de una operación industrial en tiempo real.El modelo de contabilidad en tiempo real incorpora datos desde el nivel de activos de equipos instalados, hasta niveles superiores como la unidad de proceso, el área de planta o la empresa en su conjunto. Las pantallas de operación presentan los resultados en forma de gráficos para que los operadores vean cómo sus decisiones pueden mejorar significativamente la rentabilidad.
Si nos visitas de México, por favor visita el sitio local para conocer nuestras soluciones. Si nos visita de Centroamérica, puedes conocer más de nuestra oferta en el sitio local de la región.
Añadir comentario