En promedio, los motores eléctricos consumen aproximadamente el 60% de la electricidad producida para apoyar a las industrias manufactureras; en el caso de las industrias pesadas, esta cifra aumenta al 90%. Sin embargo, muchas veces no se aplican los principios modernos de gestión de la energía para ayudar a reducir el consumo.
En todas las industrias manufactureras, los motores eléctricos desempeñan un papel crucial en el accionamiento de activos de infraestructura críticos, como cintas transportadoras, bombas, compresores, agitadores, ventiladores y otros. Pero a pesar de su papel operativo clave, los enfoques tradicionales de gestión de motores a menudo no logran optimizar el rendimiento. En algunos casos, se utilizan enfoques de apoyo fragmentados que sólo se centran en los motores individuales, en lugar de adoptar una visión más integrada y holística. En otros casos, el mantenimiento del motor es reactivo. Sólo después de que se producen casos de tiempo de inactividad se reúnen los recursos para abordar el problema y los retrasos posteriores son costosos.
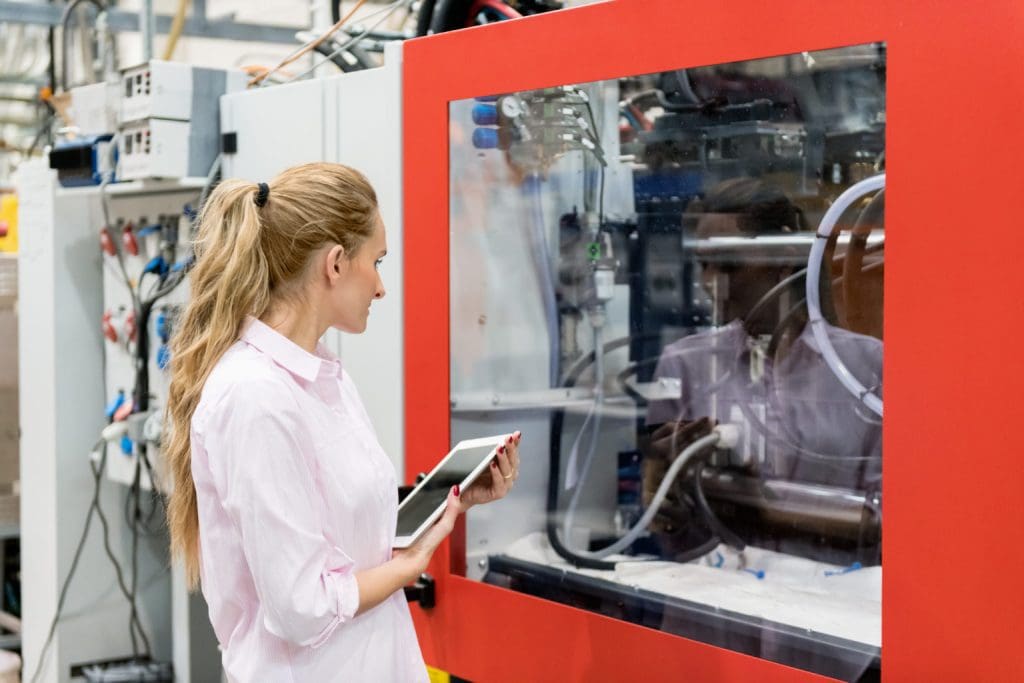
Los operadores de plantas de hoy enfrentan el desafío de controlar mejor los costos de energía del motor y al mismo tiempo mantener la resiliencia operativa. Desde paradas de plantas, daños a los equipos y riesgos para las personas o incluso el medio ambiente, la falla del motor puede resultar bastante costosa.
Tener una estrategia que integre soluciones de protección y control de motores puede ayudar a las plantas a reducir costos y aumentar la producción simultáneamente. Una conexión y comunicación sólidas entre el motor y los sistemas de automatización desempeñan un papel importante a la hora de minimizar los casos de fallo del motor. Además, los costos energéticos generales se reducen cuando se monitorean los datos energéticos de los motores para que la función pueda alinearse mejor con la carga de trabajo.
Habilitadores claves para migrar a la gestión avanzada de motores
Implementar una estrategia de gestión de motores más holística requiere una planificación cuidadosa y la combinación adecuada de tecnologías. Tradicionalmente, la mayoría de las empresas no han logrado integrar el control de motores, la automatización y los sistemas de energía debido a las complejidades técnicas percibidas. Afortunadamente, gracias a los avances tecnológicos y las nuevas tendencias como la digitalización y el Internet industrial de las cosas (IIoT), la conectividad avanzada hace que la implementación de una estrategia integral de gestión de motores sea asequible y factible. Los elementos clave que impactan una estrategia de gestión motora más avanzada incluyen:
- Herramientas sencillas orientadas a aplicaciones: para los fabricantes de máquinas que obtienen muchas de las soluciones motorizadas, la eficiencia aumenta cuando los componentes principales de la máquina son fáciles de seleccionar, instalar, cablear, poner en marcha y pueden recibir mantenimiento de forma remota. Al diseñar y configurar una solución, en lugar de acceder a varios catálogos para identificar productos para construir una arquitectura de administración de motores (por ejemplo, disyuntores, contactores, relés de sobrecarga, variadores) y luego escribir los números de pieza adecuados para realizar pedidos, las herramientas de configuración automatizadas ahora permiten OEM, cuadristas e incluso usuarios finales para generar soluciones rápidas e integrales. Estas herramientas han demostrado reducir el tiempo de diseño y selección hasta en un 40%. Para aplicaciones de la industria pesada, el diseño eléctrico se ve afectado por motores grandes. La capacidad de evaluar el tamaño necesario del transformador, seleccionar una solución inicial o abordar la mejora de la calidad de la energía es fundamental para tomar las decisiones tempranas de diseño correctas, dando forma a la instalación y su evolución en el tiempo. Las herramientas de ingeniería adecuadas diseñadas en torno a estas necesidades son la respuesta a dichas limitaciones.
- Capacidad de recopilar datos de rendimiento energético: cuando los dispositivos, como los variadores orientados a servicios Altivar Process, se conectan a motores, están equipados con la inteligencia para operar el motor en el mejor punto de eficiencia para ayudar a reducir el consumo eléctrico en al menos un 30 %. Además, los arrancadores de motor inteligentes, como Tesys Island, y las soluciones de gestión de carga digital facilitan mucho la optimización del rendimiento de la máquina. Cada alimentador de carga puede proporcionar datos de activos para optimizar la máquina y el proceso, así como también proporcionar datos reales de la corriente de línea. Estos dispositivos ofrecen a los fabricantes de máquinas la opción de monitorear de forma remota los dispositivos instalados y brindar a sus clientes un servicio de mantenimiento predictivo basado en la nube y, en última instancia, monetizar los datos de activos de carga recientemente accesibles.
- Análisis de software: con las soluciones inteligentes de gestión de motores implementadas, el personal de mantenimiento ya no necesita estar cerca de los componentes de los activos para solucionar problemas. Las situaciones anormales pueden abordarse antes de que se vuelvan críticas y provoquen una parada de producción mediante una prealarma que se basa en parámetros de comportamiento preestablecidos. Los datos recopilados se combinan y analizan con soluciones de software dedicadas, como EcoStruxure Asset Advisor, para poder predecir el rendimiento futuro de los activos del cliente. El costo total de propiedad se puede optimizar con análisis avanzados para identificar posibles modos de falla a través de paneles web procesables, informes de cronograma y recomendaciones con soporte operativo para las personas en el sitio.
Para más información, visite nuestro sitio web de gestión de motores para obtener más información sobre las arquitecturas de soluciones de gestión de motores digitalizadas que ayudan a mejorar el rendimiento del motor y la eficiencia energética.
Añadir comentario