En esta serie de 2 publicaciones de blogs, analizaremos la última tecnología de supervisión basada en el estado para equipos rotativos.
Primero, me gustaría hablar sobre la necesidad urgente de que las empresas industriales encuentren una solución mejor que las soluciones tradicionales de supervisión de motores.
En mi próxima publicación analizaré detenidamente cómo el Motor Current Signature Analysis (MCSA) está respondiendo a esta necesidad.
Reducir el costoso tiempo de parada: un reto para toda la industria
La información disponible indica que los costes del tiempo de parada en la industria se sitúan en una media de entre 25 000 y 40 000 € por hora.
Sin embargo, para algunas industrias como la fabricación de automóviles, estos costes pueden llegar a los 42 000 € por minuto. Se relacionan con pérdidas de ingresos, costes de recuperación y, en algunos casos, sanciones y multas basadas en acuerdos o regulaciones de nivel de servicio.
Los fallos de los motores eléctricos son una causa común de tiempo de parada no planificado. La maquinaria rotativa accionada por motores de inducción de CA de baja o media tensión representa la mayoría de las aplicaciones industriales, desde oil&gas hasta minería, marítimo, aeropuertos y centros logísticos.
Además de los motores, los equipos rotativos pueden incluir bombas, compresores, transportadores, soplantes o ventiladores, rodillos o molinos, etc.
Dado que entre el 20 y el 25 % de los motores eléctricos son fundamentales para las operaciones, y que la tasa de fallos anual típica es de hasta el 7 %, los motores tienen un gran impacto en el tiempo de parada y las pérdidas.
Además, las reparaciones necesarias a menudo se realizan durante las horas de operación, lo que provoca un mayor tiempo de parada.
La Oficina de Tecnologías Industriales del Departamento de Energía de EE. UU. estima que los motores representan el 60 % del consumo de energía eléctrica en las industrias manufactureras y hasta el 90 % en las industrias de alto consumo eléctrico. Por lo tanto, encontrar formas de mejorar la eficiencia puede representar una gran diferencia en los resultados de una empresa.
Por estas razones, las organizaciones deben comenzar a adoptar una estrategia de mantenimiento más predictiva que ayude a evitar reparaciones y tiempo de parada no programados, y que mejore la eficiencia, reduzca los costes y prolongue la vida útil de los equipos rotativos.
Para ello es necesario contar con el apoyo de la supervisión basada en el estado y el análisis predictivo.
Mantenimiento predictivo frente al mantenimiento tradicional de motores
En el entorno industrial se utilizan diversas estrategias de mantenimiento.
Si el equipo de una instalación utiliza el método de «funcionamiento hasta que falle», básicamente se realiza un mantenimiento mínimo o nulo hasta que el motor falla por completo.
Obviamente, la organización debe aceptar el tiempo de parada no planificado como parte de sus operaciones regulares. Si se utiliza una estrategia preventiva, el mantenimiento se realiza a intervalos establecidos según el calendario o las horas de funcionamiento.
El objetivo será lograr un nivel de disponibilidad basado en estadísticas de tiempo medio entre fallos.
Desafortunadamente, esto significa que el mantenimiento a menudo se realiza demasiado tarde, después de un fallo costoso, o demasiado pronto, lo que puede generar gastos operativos innecesarios.
Y, en última instancia, ninguna de estas estrategias tiene en cuenta el estado real del motor.
Un enfoque mucho mejor es el mantenimiento predictivo, en el que se trabaja solo cuando el motor lo necesita, es decir, cuando el rendimiento se degrada o se predice un fallo.
Sin embargo, este enfoque requiere un control continuo del estado del motor. En el mejor de los casos, la tecnología debe detectar los riesgos en una fase temprana.
Algunos ejemplos de condiciones de riesgo: degradación de los rodamientos, excentricidades del rotor o del acoplamiento, desequilibrio mecánico, aflojamiento del devanado del estátor, cavitación de la bomba, perturbación por armónicos o desalineación del eje.
Es importante detectar este tipo de riesgos con anticipación para reducir el daño potencial, minimizar el desperdicio de energía y, lo que es más importante, minimizar el tiempo de parada no planificado.
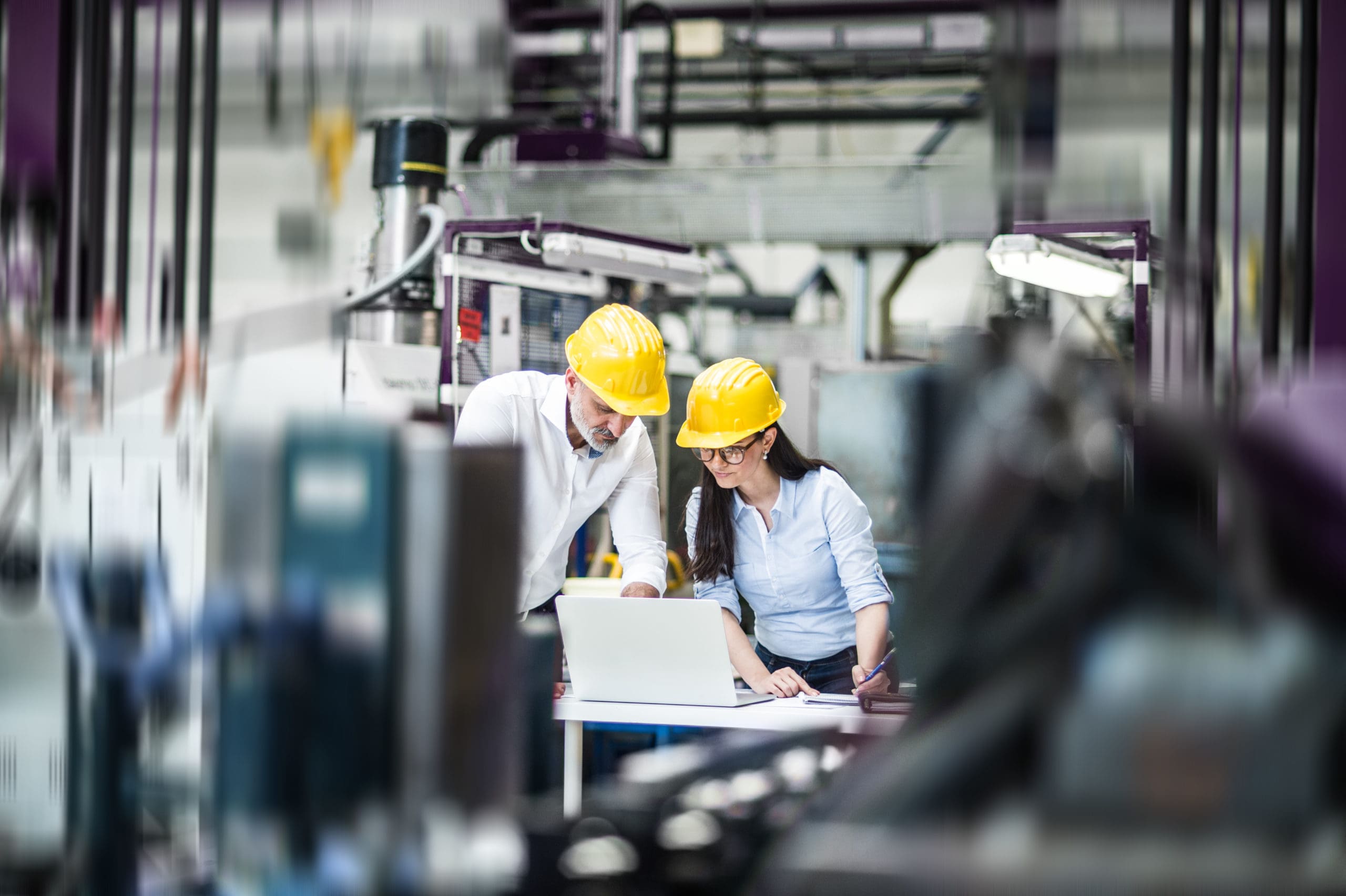
Problemas con la tecnología tradicional de supervisión de motores
Para supervisar la condición de los motores se han utilizado diversos métodos, algunos de los cuales se remontan a muchas décadas. Cada uno tiene sus ventajas, pero la mayoría, también debilidades importantes.
Ejemplo:
- Los sensores de vibración pueden desajustarse por el ruido o las vibraciones del entorno.
- El análisis de aceite y el análisis de vibraciones no pueden detectar problemas eléctricos
- Los sensores acústicos son sensibles al ruido de fondo y a la interferencia de otros objetos
- Las cámaras termográficas requieren una línea de visión directa a los objetos de interés y son sensibles a la temperatura ambiente y a las propiedades termo ópticas de los objetos supervisados.
En todas las tecnologías anteriores, los sensores deben colocarse en o cerca del equipo a supervisar, lo que significa que no se pueden utilizar con motores en lugares inaccesibles, como los empleados en el drenaje subterráneo, sumergidos en el casco de un barco o alojados dentro de máquinas más grandes.
Tampoco son ideales para equipos ubicados a distancia o muy espaciados, como los aerogeneradores marinos, ya que la instalación de los sensores será difícil, lenta y costosa.
Además, estos sensores deben ser alimentados por una fuente de alimentación cableada o por una batería que requiera una sustitución periódica.
Por último, este tipo de sensores puede resultar dañado si se utiliza en entornos exigentes, como un transportador que mueve placas de acero calientes, o zonas ATEX con atmósferas explosivas.
En los últimos años, ha surgido una nueva tecnología denominada Motor Current Signature Analysis (MCSA) que ofrece grandes ventajas sobre las técnicas mencionadas anteriormente.
El MCSA es una tecnología innovadora basada en inteligencia artificial que supervisa las señales eléctricas que alimentan los motores de CA y compara las condiciones con una biblioteca de huellas digitales de datos.
Entre sus ventajas destacan: una instalación más sencilla en una gama más amplia de aplicaciones, menos fallos en los equipos, una vida útil más prolongada, un menor coste total de propiedad y un período de amortización más corto.
En mi próxima publicación, analizaremos con detalle esta emocionante innovación.
Obtenga más información sobre la supervisión basada en el estado
Como parte de nuestro completo portafolio de soluciones de gestión de motores, EcoStruxure Asset Advisor for Electrical Distribution ahora incluye la supervisión basada en el estado de equipos rotativos utilizando tecnología MCSA.
Nuestra solución totalmente integrada y certificada incluye sensores de motor instalados dentro del MCC y conectados a la nube a través de dispositivos de adquisición de datos y pasarelas específicos, con una arquitectura completa que cumple las estrictas directrices de ciberseguridad.
La solución ofrece alarmas, un panel de control integrado y el apoyo de nuestros asesores expertos.
Conoce también las mejores prácticas de gestión del rendimiento de equipos o prueba nuestra calculadora de ROI de gestión del rendimiento de equipos.
Añadir comentario