El valor añadido generado dentro de cada fase del ciclo de vida de un producto ha evolucionado a lo largo de los últimos años, en los que ha habido una relocalización de la fabricación y por lo tanto se ha extendido por todo el mundo las tecnologías de manufactura más avanzadas y los estándares de calidad más estrictos.
Para representar este hecho podemos usar el concepto de “smiling curve”, que promulgó el fundador de la compañía Acer, Stan Shih en la década de los 90, pero que se mantiene perfectamente válido para la industria actual. En esta representación destacan como principales aportadores al valor final del producto, las fases de I+D+i y diseño y márketing y servicios mientras que el lugar de fabricación del equipo es lo menos diferencial, ya que la calidad de construcción se ha convertido en una commodity, es decir, el comprador ya la presupone.
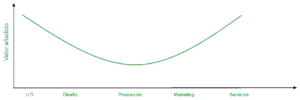
Es ya un hecho comprobado que la digitalización permite al fabricante de maquinaria mejorar cada una de las fases del ciclo de vida del producto. La inversión en la digitalización del proceso productivo es muy importante ya que es dónde radican una gran parte de los costes del producto, así como el impacto ambiental de este. Pero si miramos de nuevo la smiling curve, cabría pensar ¿si la digitalización es importante para mejorar la fase de fabricación, también podría ser beneficiosa para las fases que generan más valor añadido? Pues la respuesta es sí, rotundamente.
¿Por qué digitalizar todo el ciclo productivo?
Los beneficios de la digitalización en las fases de I+D, diseño, marketing y servicios pueden ser fruto de la automatización de procesos, de sistemas de simulación o de la gestión digital del conocimiento, por citar algunas funcionalidades digitales con gran impacto en estas fases. Pero la funcionalidad digital transversal a todas las fases es la capacidad de ver lo que está pasando en tu base instalada. Con esta información, los datos en vivo de producción, el fabricante de maquinaria será capaz de generar servicios de alto valor añadido para el usuario del activo mejorando sustancialmente el margen de su actividad, o , si nos centramos en las primeras fases, sería capaz de detectar rápidamente nuevas necesidades en sus clientes o bien detectar rápidamente mejoras para sus productos e implementarlas rápidamente, reduciendo el time-to-market en un 50% ganando, por lo tanto, capacidad de adaptación al mercado. Si seguimos el ejemplo que pusimos en el post anterior, el impacto de optimizar el tamaño de los actuadores puede suponer una reducción de hasta un 30% en el tamaño de los mismos, suponiendo una reducción importante en el coste y el footprint (espacio que ocupa en planta) de la máquina.
Por lo tanto, además de las posibles mejoras operativas, más relacionadas con procesos internos en la empresa, la transformación digital de los fabricantes de maquinaria repercutirá directamente sobre la capacidad de crear productos y servicios de alto valor añadido para sus clientes.
Con el objetivo de contar con los datos necesarios que para conseguir los objetivos expuestos en este post, la máquina ha de ser capaz de transmitir los datos de actividad de manera cibersegura, gracias a PLC con capacidad de cifrado de la información, como el Modicon M262. Por otra parte, la información emitida por las máquinas se ha de contener en una plataforma de servicios basada en cloud como EcoStruxure Machine Advisor. Gracias a este sistema podrás monitorizar los datos de rendimiento y analizar en detalle el comportamiento de tus máquinas en todo el mundo de forma remota y segura.
Añadir comentario